Progress of aerospace-based spray cooling applications
- Key Laboratory of Energy Thermal Conversion and Control of Ministry of Education, School of Energy and Environment, Southeast University, Nanjing, Jiangsu, China
Introduction
The heat flux generated by electronic components increases dramatically since the integration and miniaturization of electronic components have been extensively proposed (Chen et al., 2021; Teng et al., 2022). Huge generated amounts of heat and the decrease of heat dissipation area lead to the sharp increase in heat flux of the devices (Wang et al., 2015; Wang et al., 2022a). In some specific applications such as air-borne high energy-density directional weapons, the heat flux of electronic devices has been achieved at 103 W/cm2 (Wang et al., 2021a). Thermal management becomes a key bottleneck in technology development because the service life, reliability, and stability of electronic devices are affected by the overheating caused by untimely dissipation of heat flux (Chen et al., 2022). Traditional single-phase cooling can no longer satisfy the demand of current heat dissipation, while the phase change process can absorb large amounts of heat (Hao et al., 2022), such as microchannel cooling (Zhang et al., 2021), jet impingement (Overholt et al., 2005) and spray cooling (Wang et al., 2017), which are now considered as highly-efficient methods that can take away a large amount of heat. Spray cooling is considered to have the advantages of large specific surface area, small coolant flow rate, small temperature difference between surface area and working medium, and high heat flux removal ability comparing other cooling methods (Wang et al., 2018c). Therefore, spray cooling technology has always been a hot technology in the field of electronic cooling, especially in the aerospace field with high heat dissipation requirements such as diode array, large radar, laser transmitter, and satellite electronics (Wang J. X. et al., 2016) as shown in Figure 1A,B. Thus, the operating principles, the influence factors, and prospects for aerospace-oriented spray cooling research have been reviewed in this paper.
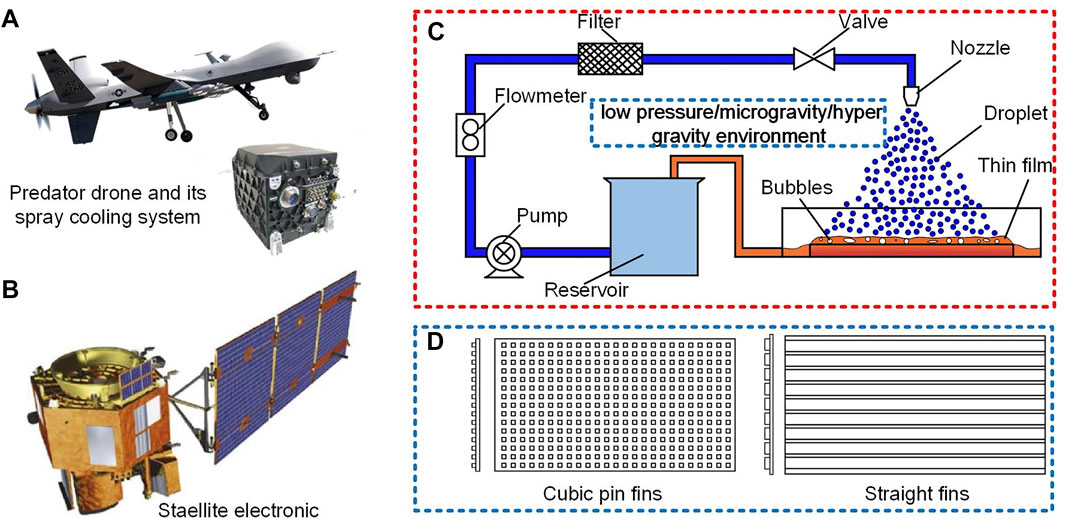
FIGURE 1. (A) and (B) application of spray cooling in aerospace field (Liang and Mudawar, 2017); (C) the principle diagram of spray cooling system; (D) enhanced heat transfer surface structures.
The operating principles of spray cooling
The operating principle of spray cooling is a technology in which the coolant is atomized into small droplets to dissipate heat on the hot surface when passing through the high-pressure nozzle as shown in Figure 1C (Wang J. et al., 2021). According to the different temperatures of the heated wall, the domain heat transfer mechanism of spray cooling is different (Zhao et al., 2010). When the surface temperature is under boiling point, a thin liquid film is formed on the wall due to the continuous impact of droplets, and forced convection in the liquid film plays an important role in heat transfer. Pautsch and Shedd. (2006) used a non-intrusive total-internal-reflection-based optical technique and fundamental equations of geometric optics to measure the film thickness and found that the thickest film area has poor heat transfer, and the liquid film far away from the spray area will evaporate and dry quickly, resulting in heat transfer deterioration. When the temperature of the hot surface exceeds the boiling point of the coolant, phase change will happen inside the liquid film, and the dominant mode of heat transfer mechanism of spray cooling turns to nuclear boiling (Qiu et al., 2017). Nuclear boiling of spray cooling is similar to pool boiling in that the gasification core is first generated on the hot wall, then bubbles are formed and gradually separated from the surface. However, it is worth noting that the droplet impact of spray cooling cause liquid film internal disturbance to accelerate the bubbles escaping velocity, resulting in the higher spray cooling heat transfer efficiency. In addition, secondary nucleation is also the reason for the high heat transfer efficiency of spray cooling (Selvam et al., 2009), which is considered that a large amount of vaporization core is brought into the liquid film when the droplet impacts the liquid film, thus enhancing the heat transfer. When the temperature of the wall continues to rise, the bubbles generated cannot escape the wall in time and form a vapor film on the wall to prevent the new coolant from cooling the wall, which means that the cooling state has reached the critical heat flux (CHF) (Hou et al., 2013). The occurrence of CHF is an important reason to limit the development of spray cooling.
Influence factors in the aerospace field
Gravity and vibratory effect
In the aerospace field, spray cooling is often used in high-altitude airspace or space environments where the operating environment of spray cooling is rather different from that of near-ground applications. Thus, the influence of the gravity field must be considered (Sinha-Ray et al., 2014; Sinha-Ray and Yarin, 2014). The influence of gravity on heat flux under different flow rates and nozzle heights was experimentally discussed (Zhang et al., 2016). The results showed that increasing gravity loads improved heat flux in most cases, but had little effect at high flow rates and low nozzle height. A two-dimensional model was developed to study the temperature of a flat heated surface under different loads and the researchers found that the temperature of the wall surface under high overload was lower than that under normal gravity when the droplet velocity is 4 m/s (Pang et al., 2017). At present, the effect of gravity on spray cooling is still very vague, which leads to inconsistent conclusions from different studies. In addition to a lack of theoretical knowledge, the duration of an artificial space gravity environment (such as a falling tower, or parabolic flight) is relatively short (only a few seconds), which brings great uncertainty to its research (Wang et al., 2020). Another consideration in the aerospace field is the vibration field, a two-dimensional VOF model was utilized to study the influence of wall vibration conditions on heat transfer (Wang Z. et al., 2016). The results showed that high frequency and high amplitude would weaken heat transfer in the case of light droplet impact, while vibration would enhance heat transfer in the case of dense droplet impact. Currently, it is still a hot research area to explore the effect of vibration on spray cooling.
Low-pressure environment effect
Low environmental pressure is another influencing factor in high-altitude flight, which leads to the decrease of the saturation temperature of the working medium, facilitating a superheated state of the coolant after leaving the nozzle (Wang et al., 2018b). This will produce two instantaneous evaporation states: (1) the instantaneous evaporation/boiling of the droplet; (2) flash/boiling of the film covering the target surface (Cheng et al., 2015). The first phenomenon occurs when the droplet leaves the nozzle and is called the secondary breakup process due to the formation of bubbles inside the droplet (Wang et al., 2020). There are two main driving forces for secondary breakup process generation in droplet instantaneous evaporation/boiling process: (1) the initial temperature difference of the droplet (Chen et al., 2018); (2) bubbles produced in the droplet (Zeng and Lee, 2001). The second phenomenon occurs in the saturated film which can absorb lots of heat by using the latent heat of coolant. Based on the influence of environmental pressure on spray cooling, a one-dimensional mathematical model of liquid nitrogen flash spray cooling for thermal control of electronic equipment cabin of the near-space vehicle was proposed (Wang C. et al., 2018), where the ambient pressure was maintained below 5,530 Pa. The optimal operating conditions were determined, which is instructive for practical application.
Enhancement of spray cooling in the aerospace field
There are four main ways to increase the heat transfer effect of spray cooling: (1) exert external multi-physics physic fields; (2) promote larger area of heat transfer; (3) enhance coolant thermal properties. Shahriari et al. (2016) found the Leidenfrost effect can be limited and film boiling can be suppressed by adding an external electric field, which can increase the bubble escape rate and thus, enhance heat transfer. Sapit et al. (2019) used a fine nozzle to obtain a higher discharge rate of the sprayed coolant, creating a larger heat transfer area and attaining an enhanced heat transfer. Besides, surface treatment is one of the commonly used method to increase heat transfer area (Zhang et al., 2015). Finned surfaces (Rao, 2018), nano-/micro-structured surfaces (Hou et al., 2014; Oh et al., 2018), and porous-material-assisted functional surfaces (Jun et al., 2016) have been proven to enhance heat transfer, which all increased the contact area between coolant and heated surface as shown in Figure 1D. Liu et al. (2018) added millimeter-scale geometric structures (square fin, triangular fin, and straight groove fin) to the smooth surface and found that all three mm-scale microstructures can increase the heat flux of spray cooling, with the straight groove fin having the best effect, followed by square fin and triangular fin. Enhancing coolant thermal properties is another method to enhance heat transfer, such as nano-fluid (Riazi et al., 2016), saline solution (Cui et al., 2003), surfactant (Hsieh et al., 2015), which change the physical properties of the initial working medium, such as latent heat, thermal conductivity, surface tension, contact angle, etc. Most recently, Wang et al. (2018b) found that an immersed spray cooling could obtain an enhanced heat transfer because of the sufficient coolant supply and strong disturbance effect.
Perspectives of spray cooling in the aerospace field
Compared with the spray cooling technology on the ground, there are fewer publications in the aerospace field, mainly due to the difficult experimental conditions and high experimental cost. The United States Air Force Research Laboratory began to study spray cooling systems after it was proposed in the aerospace thermal management field in 2008 (Silk et al., 2008). Zhang et al. (2015) concluded that the spray cooling system with an ejector condenser was a promising prototype that intelligently collects and circulates coolant by effectively transporting two-phase flow through the ejector in a complex gravitational field in China. The research of airborne spray cooling systems is the key to the sustained and reliable operation of airborne technology in complex space or high-altitude air environments. Much more attention should be paid to it. In addition, how to adjust the flow of the working medium according to the thermal load so that the temperature of electronic components can be controlled within the range need to be explored in the future. At the present, a machine learning (ML) algorithm has been successfully applied in the spray cooling field (Wang et al., 2019). Machine learning mainly uses the training dataset to train the neural network model where the pattern of the focused spray cooling system can be learnt. Researches showed that machine learning can provide accurate prediction for complex thermal-fluid system due to high reliability. Wang et al. (2019) used a backpropagation neural network method to predict the thermal performance both in flash-boiling and subcooled regions with six parameters input and the error of ±7% was observed. Moreover, a transient thermal performance prediction was also developed using ML (Wang et al., 2021b) which paves the way for ML-based temperature control of spray cooling as computational capabilities have been sufficiently developed (Wang et al., 2022b; Cao et al., 2022).
Conclusion
This paper introduces the heat transfer mechanism of spray cooling, its unique influencing factors, and challenges in the aerospace field, and also describes the methods to strengthen the heat transfer. Gravity field, vibratory field, and lower pressure were considered as the influencing factors. However, there is still no completely convincing conclusion about the influence of gravity on spray cooling. How to obtain accurate experimental data is still a key problem to solve. This paper aims to provide a further understanding of spray cooling in the aerospace field for readers and promote the application of spray cooling in the aerospace field.
Author contributions
SW contributed to conception of the study. XC wrote the first draft of the manuscript. All authors contributed to manuscript revision, read, and approved the submitted version.
Funding
This work is supported by the National Natural Science Foundation of China (No. 52106114) and Natural Science Foundation of Jiangsu Province (Grant No. BK20210239).
Conflict of interest
The authors declare that the research was conducted in the absence of any commercial or financial relationships that could be construed as a potential conflict of interest.
Publisher’s note
All claims expressed in this article are solely those of the authors and do not necessarily represent those of their affiliated organizations, or those of the publisher, the editors and the reviewers. Any product that may be evaluated in this article, or claim that may be made by its manufacturer, is not guaranteed or endorsed by the publisher.
References
Cao, X., Hao, G., Li, Y.-Y., Wang, M., and Wang, J.-X. (2022). On male urination and related environmental disease transmission in restrooms: From the perspectives of fluid dynamics. Sustain. Cities Soc. 80, 103753. doi:10.1016/j.scs.2022.103753
Chen, Q., Kum, J. M., Li, Y., and Chua, K. J. (2018). Experimental and mathematical study of the spray flash evaporation phenomena. Appl. Therm. Eng. 130, 598–610. doi:10.1016/j.applthermaleng.2017.11.018
Chen, X., Chen, S., Zhang, Z., Sun, D., and Liu, X. (2021). Heat transfer investigation of a flat-plate oscillating heat pipe with tandem dual channels under nonuniform heating. Int. J. Heat Mass Transf. 180, 121830. doi:10.1016/j.ijheatmasstransfer.2021.121830
Chen, X., Liu, X., Xu, D., and Chen, Y. (2022). Thermal performance of a tandem-dual-channel flat-plate pulsating heat pipe applicable to hypergravity. Int. J. Heat Mass Transf. 189, 122656. doi:10.1016/j.ijheatmasstransfer.2022.122656
Cheng, W.-L., Chen, H., Hu, L., and Zhang, W.-W. (2015). Effect of droplet flash evaporation on vacuum flash evaporation cooling: Modeling. Int. J. Heat Mass Transf. 84, 149–157. doi:10.1016/j.ijheatmasstransfer.2014.12.078
Cui, W., Chanda, S., and Mccahan, S. (2003). The effect of dissolving salts in water sprays used for quenching a hot surface: Part 1 - boiling of single droplets. J. Heat. Transf. 125, 326–332. doi:10.1115/1.1532010
Hao, G., Yu, C., Chen, Y., Liu, X., and Chen, Y. (2022). Controlled microfluidic encapsulation of phase change material for thermo-regulation. Int. J. Heat Mass Transf. 190, 122738. doi:10.1016/j.ijheatmasstransfer.2022.122738
Hou, Y., Liu, X., Liu, J., Li, M., and Pu, L. (2013). Experimental study on phase change spray cooling. Exp. Therm. Fluid Sci. 46, 84–88. doi:10.1016/j.expthermflusci.2012.11.023
Hou, Y., Tao, Y., and Huai, X. (2014). The effects of micro-structured surfaces on multi-nozzle spray cooling. Appl. Therm. Eng. 62, 613–621. doi:10.1016/j.applthermaleng.2013.10.030
Hsieh, S.-S., Leu, H.-Y., and Liu, H.-H. (2015). Spray cooling characteristics of nanofluids for electronic power devices. Nanoscale Res. Lett. 10, 139. doi:10.1186/s11671-015-0793-7
Jun, S., Wi, H., Gurung, A., Amaya, M., and You, S. M. (2016). Pool boiling heat transfer enhancement of water using brazed copper microporous coatings. J. Heat. Transf. 138, 071502. doi:10.1115/1.4032988
Liang, G., and Mudawar, I. (2017). Review of spray cooling – Part 1: Single-phase and nucleate boiling regimes, and critical heat flux. Int. J. Heat Mass Transf. 115, 1174–1205. doi:10.1016/j.ijheatmasstransfer.2017.06.029
Liu, X., Liu, J., Xue, R., Chen, L., and Hou, Y. (2018. Heat transfer optimization of R134a phase change spray cooling in a closed loop system. Exp. Therm. Fluid Sci. 92, 248–258.
Oh, J., Zhang, R., Shetty, P. P., Krogstad, J. A., Braun, P. V., Miljkovic, N., et al. (2018). Thin film condensation on nanostructured surfaces. Adv. Funct. Mat. 28, 1707000. doi:10.1002/adfm.201707000
Overholt, M. R., McCandless, A., Kelly, K. W., Becnel, C. J., and Motakef, S. (2005“Micro-jet arrays for cooling of electronic equipment,” in International conference on nanochannels, microchannels, and minichannels, 41855, 249–252.
Pang, L., Luo, K., Guo, Q., Li, S., and Yang, C. (2017). Numerical study of high-overload effect on liquid film of spray cooling. Appl. Therm. Eng. 127, 1015–1024. doi:10.1016/j.applthermaleng.2017.07.209
Pautsch, A. G., and Shedd, T. A. (2006). Adiabatic and diabatic measurements of the liquid film thickness during spray cooling with FC-72. Int. J. Heat Mass Transf. 49, 2610–2618. doi:10.1016/j.ijheatmasstransfer.2006.01.024
Qiu, L., Dubey, S., Choo, F. H., and Duan, F. (2017). The statistical analysis of droplet train splashing after impinging on a superheated surface. J. Heat. Transf. 139, 052201. doi:10.1115/1.4035661
Rao, Y. (2018). Jet impingement heat transfer in narrow channels with different pin fin configurations on target surfaces. J. Heat. Transf. 140, 072201. doi:10.1115/1.4039015
Riazi, H., Murphy, T., Webber, G. B., Atkin, R., Tehrani, S. S. M., Taylor, R. A., et al. (2016). Specific heat control of nanofluids: A critical review. Int. J. Therm. Sci. 107, 25–38. doi:10.1016/j.ijthermalsci.2016.03.024
Sapit, A., Razali, M. A., Mohammed, A. N., and Manshoor, B. (2019. Study on mist nozzle spray characteristics for cooling application. Int. J. Integr. Eng. 11 (3).
Selvam, R. P., Sarkar, M., Sarkar, S., Ponnappan, R., and Yerkes, K. L. (2009). Modeling thermal-boundary-layer effect on liquid-vapor interface dynamics in spray cooling. J. Thermophys. Heat Transf. 23, 356–370. doi:10.2514/1.34982
Shahriari, A., Hermes, M., and Bahadur, V. (2016. Electrical control and enhancement of boiling heat transfer during quenching. Appl. Phys. Lett. 108 (9), 091607.
Silk, E. A., Golliher, E. L., and Selvam, R. P. (2008). Spray cooling heat transfer: Technology overview and assessment of future challenges for micro-gravity application. Energy Convers. Manag. 49, 453–468. doi:10.1016/j.enconman.2007.07.046
Sinha-Ray, S., Sinha-Ray, S., Yarin, A. L., Weickgenannt, C. M., Emmert, J., Tropea, C., et al. (2014). Drop impact cooling enhancement on nano-textured surfaces. Part II: Results of the parabolic flight experiments [zero gravity (0g) and supergravity (1.8g)]. Int. J. Heat. Mass Transf. 70, 1107–1114. doi:10.1016/j.ijheatmasstransfer.2013.11.008
Sinha-Ray, S., and Yarin, A. L. (2014). Drop impact cooling enhancement on nanotextured surfaces. Part I: Theory and results of the ground (1 g) experiments. Int. J. Heat. Mass Transf. 70, 1095–1106. doi:10.1016/j.ijheatmasstransfer.2013.11.007
Teng, Z., Zhong, M., Mao, Y., Li, E., Guo, M., Wang, J.-X., et al. (2022). A concentrated sunlight energy wireless transmission system for space solar energy harvest. Energy Convers. Manag. 261, 115524. doi:10.1016/j.enconman.2022.115524
Wang, C., Song, Y., and Jiang, P. (2018a). Modelling of liquid nitrogen spray cooling in an electronic equipment cabin under low pressure. Appl. Therm. Eng. 136, 319–326. doi:10.1016/j.applthermaleng.2018.02.095
Wang, J.-X., Guo, W., Xiong, K., and Wang, S.-N. (2020). Review of aerospace-oriented spray cooling technology. Prog. Aerosp. Sci. 116, 100635. doi:10.1016/j.paerosci.2020.100635
Wang, J.-X., Li, Y.-Z., Li, G.-C., and Ji, X.-Y. (2019). Ground-based near-space-oriented spray cooling: Temperature uniformity analysis and performance prediction. J. Thermophys. Heat Transf. 33, 617–626. doi:10.2514/1.t5547
Wang, J.-X., Li, Y.-Z., Li, G.-C., Xiong, K., and Ning, X. (2017). Investigation of a gravity-immune chip-level spray cooling for thermal protection of laser-based wireless power transmission system. Int. J. Heat Mass Transf. 114, 715–726. doi:10.1016/j.ijheatmasstransfer.2017.06.111
Wang, J.-X., Li, Y.-Z., Yu, X.-K., Li, G.-C., and Ji, X.-Y. (2018b). Investigation of heat transfer mechanism of low environmental pressure large-space spray cooling for near-space flight systems. Int. J. Heat Mass Transf. 119, 496–507. doi:10.1016/j.ijheatmasstransfer.2017.11.128
Wang, J.-X., Li, Y.-Z., Zhang, H.-S., Wang, S.-N., Mao, Y.-F., Zhang, Y.-N., et al. (2015). Investigation of a spray cooling system with two nozzles for space application. Appl. Therm. Eng. 89, 115–124. doi:10.1016/j.applthermaleng.2015.05.082
Wang, J.-X., Li, Y.-Z., Zhang, Y., Li, J.-X., Mao, Y.-F., Ning, X.-W., et al. (2018c). A hybrid cooling system combining self-adaptive single-phase mechanically pumped fluid loop and gravity-immune two-phase spray module. Energy Convers. Manag. 176, 194–208. doi:10.1016/j.enconman.2018.09.010
Wang, J.-X., Li, Y.-Z., Zhong, M.-L., and Zhang, H.-S. (2021a). Investigation on a gas-atomized spray cooling upon flat and micro-structured surfaces. Int. J. Therm. Sci. 161, 106751. doi:10.1016/j.ijthermalsci.2020.106751
Wang, J.-X., Wu, Z., Zhong, M.-L., and Yao, S. (2021b). Data-driven modeling of a forced convection system for super-real-time transient thermal performance prediction. Int. Commun. Heat Mass Transf. 126, 105387. doi:10.1016/j.icheatmasstransfer.2021.105387
Wang, J.-X., Yu, W., Wu, Z., Liu, X., and Chen, Y. (2022a). Physics-based statistical learning perspectives on droplet formation characteristics in microfluidic cross-junctions. Appl. Phys. Lett. 120, 204101. doi:10.1063/5.0086933
Wang, J.-X., Zhong, M., Wu, Z., Guo, M., Liang, X., Qi, B., et al. (2022b). Ground-based investigation of a directional, flexible, and wireless concentrated solar energy transmission system. Appl. Energy 322, 119517. doi:10.1016/j.apenergy.2022.119517
Wang, J., Li, Y., Liu, X., Shen, C., Zhang, H., Xiong, K., et al. (2021c). Recent active thermal management technologies for the development of energy-optimized aerospace vehicles in China. Chin. J. Aeronautics 34, 1–27. doi:10.1016/j.cja.2020.06.021
Wang, J. X., Li, Y. Z., Wang, S. N., Zhang, H. S., Ning, X. W., Guo, W., et al. (2016a). Experimental investigation of the thermal control effects of phase change material based packaging strategy for on-board permanent magnet synchronous motors. Energy Convers. Manag. 123, 232–242. doi:10.1016/j.enconman.2016.06.045
Wang, Z., Xing, Y., Liu, X., Zhao, L., and Ji, Y. (2016b). Computer modeling of droplets impact on heat transfer during spray cooling under vibration environment. Appl. Therm. Eng. 107, 453–462. doi:10.1016/j.applthermaleng.2016.06.176
Zeng, Y., and Lee, C. F. F. (2001). An atomization model for flash boiling sprays. Combust. Sci. Technol. 169, 45–67. doi:10.1080/00102200108907839
Zhang, C., Li, G., Sun, L., and Chen, Y. (2021). Experimental study on active disturbance rejection temperature control of a mechanically pumped two-phase loop. Int. J. Refrig. 129, 1–10. doi:10.1016/j.ijrefrig.2021.04.038
Zhang, Y., Pang, L., Liu, M., and Xie, Y. (2016). Investigation of spray cooling: Effect of different heater surfaces under acceleration. Int. Commun. Heat Mass Transf. 75, 223–231. doi:10.1016/j.icheatmasstransfer.2015.05.011
Zhang, Z., Jiang, P.-X., Christopher, D. M., and Liang, X.-G. (2015). Experimental investigation of spray cooling on micro-nano- and hybrid-structured surfaces. Int. J. Heat Mass Transf. 80, 26–37. doi:10.1016/j.ijheatmasstransfer.2014.08.085
Keywords: spray cooling, aerospace-based, gravity effect, low-pressure, enhancement heat transfer
Citation: Chen X and Wu S (2022) Progress of aerospace-based spray cooling applications. Front. Energy Res. 10:968506. doi: 10.3389/fenrg.2022.968506
Received: 14 June 2022; Accepted: 04 July 2022;
Published: 22 July 2022.
Edited by:
Ang Li, Suzhou University of Science and Technology, ChinaReviewed by:
Xuan Wang, Tianjin University, ChinaCopyright © 2022 Chen and Wu. This is an open-access article distributed under the terms of the Creative Commons Attribution License (CC BY). The use, distribution or reproduction in other forums is permitted, provided the original author(s) and the copyright owner(s) are credited and that the original publication in this journal is cited, in accordance with accepted academic practice. No use, distribution or reproduction is permitted which does not comply with these terms.
*Correspondence: Suchen Wu, suchenwu@seu.edu.cn